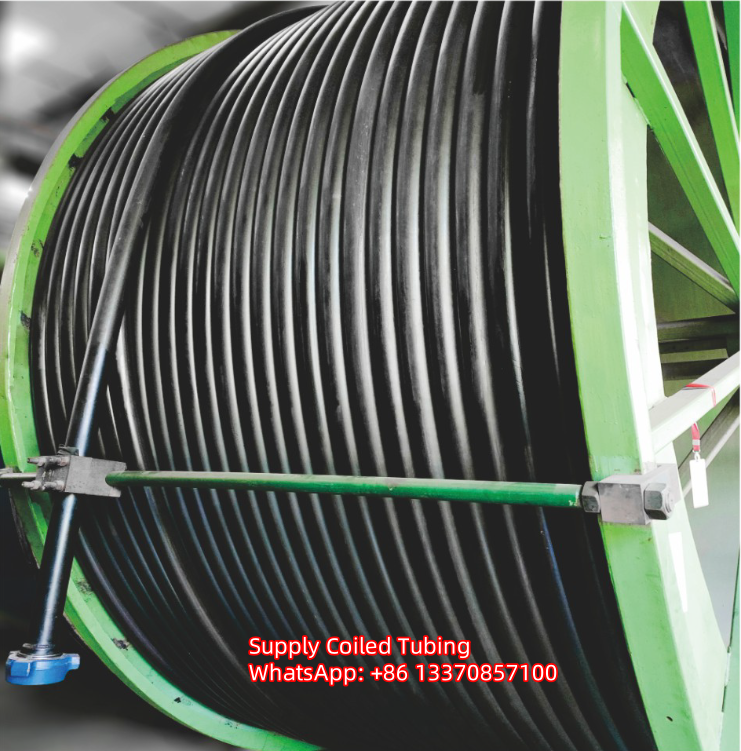
A coiled tubing string is a continuous, flexible steel or composite pipe wound on a large spool. It is used in oil and gas operations for various well intervention, completion, and drilling tasks without the need for a conventional drill pipe or workover rig.
Key Features:
Made of high-strength, low-alloy steel or composite materials.
Available in different diameters (typically 0.75 to 2.875 inches).
Can be thousands of feet long and spooled onto a reel.
Allows for real-time data transmission with fiber-optic or electric lines.
Applications:
- Well Intervention: Used for cleaning, acid stimulation, and sand control.
- Drilling & Milling: Helps with underbalanced drilling and removing obstructions.
- Logging & Perforation: Deploys logging tools and perforating guns.
- Nitrogen Injection: Assists in well kick-off and lifting fluids.
- Hydraulic Fracturing Support: Delivers proppant or fluids to stimulate production.
Advantages of Coiled Tubing:
✔ Continuous operation without pipe connections.
✔ Faster and more cost-effective than conventional methods.
✔ Can operate in live wells under pressure.
✔ Reduces downtime and rig costs.
Several factors can affect the performance and lifespan of a coiled tubing string. These include:
1.Mechanical Factors
Fatigue Life: Coiled tubing undergoes repeated bending and straightening, which causes metal fatigue and limits its lifespan.
Buckling: When pushed into highly deviated or horizontal wells, coiled tubing can buckle, reducing its effectiveness.
Wall Thickness & Ovality: Variations in wall thickness or deformation (ovality) can weaken the tubing and affect its integrity.
2.Corrosion & Chemical Effects
H2S (Hydrogen Sulfide) Exposure: Leads to sulfide stress cracking (SSC) and metal embrittlement.
CO2 & Acid Exposure: Carbon dioxide and acids (e.g., HCl, HF) can cause corrosion and pitting, reducing tubing life.
Scale & Deposits: Accumulation of scale (e.g., calcium carbonate) can restrict flow and affect operations.
3.Operational Conditions
High Pressure & Temperature: Extreme conditions can weaken the tubing and affect its elasticity.
Abrasion & Erosion: Flowing sand, proppants, or harsh fluids can erode the internal surface of the tubing.
Overloading & Exceeding Design Limits: Pulling too much tension or exceeding burst and collapse pressures can lead to failure.
4.Manufacturing & Material Quality
Weld Quality: Poorly welded seams or defects can cause early failure.
Material Composition: Higher-strength alloys improve durability but may be more expensive.
Storage & Handling: Improper spooling, exposure to moisture, or rough handling can introduce weak points.
5.Operational Procedures & Human Factors
Improper Running & Pulling Speeds: Excessive speed can cause mechanical damage.
Lack of Regular Inspections: Undetected wear or corrosion can lead to unexpected failures.
Inadequate Lubrication & Fluids: Poor lubrication increases friction and wear.