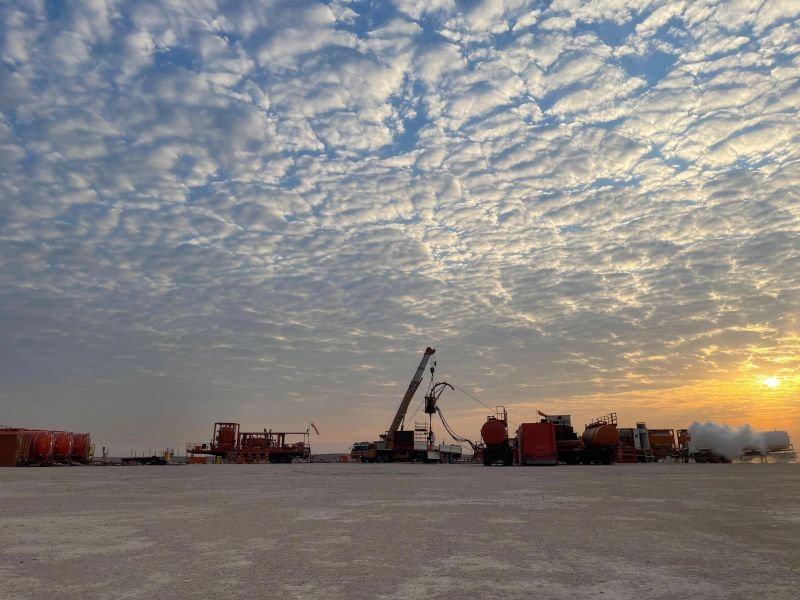
In coiled tubing milling, the load cell is essential for monitoring the weight-on-bit (WOB), providing real-time data on force applied to the downhole milling tool. Load cell issues can significantly impact operations, creating inefficiencies and risks. Key load cell issues and mitigation strategies include:
1. Impact on Weight-on-Bit (WOB) Control
Problem:
A faulty load cell may provide inaccurate WOB data, leading to excessive or insufficient force.
Consequences:
Excessive WOB: Risks bit damage, tool failure, and tubing fatigue.
Insufficient WOB: Leads to inefficient milling, slower progress, and higher costs.
Solution:
Adjust WOB based on historical data if load readings are inconsistent. Monitor pump pressure and torque as secondary indicators.
2. Risk of Stuck Pipe
Problem:
Without accurate load data, applying incorrect force can cause the tool or tubing to get stuck.
Consequences:
Stuck pipe situations can lead to downtime, requiring jarring or fishing operations.
Increased risk of damage to coiled tubing and downhole equipment.
Solution:
Regularly pull and reinsert tubing to clear debris, and monitor pressure trends for sticking tendencies.
3. Difficulty in Identifying Downhole Issues
Problem:
The load cell provides feedback on downhole resistance. Without it, detecting bit wear or formation hardness changes is harder.
Consequences:
Bit wear can go unnoticed, prolonging job time.
Solution:
Regularly check milling rate and torque as indicators of downhole conditions, and increase trip frequency to inspect the bit.
4. Increased Risk of Coiled Tubing Fatigue and Damage
Problem:
Without load data, the risk of excessive or fluctuating loads on tubing increases, potentially leading to fatigue and damage.
Consequences:
Tubing fatigue shortens lifespan, increasing the chance of pipe failure.
Damaged tubing can lead to fluid leakage or downhole parting, requiring intervention.
Solution:
Use conservative WOB, monitor fatigue cycles, and regularly check surface equipment to ensure safe tubing operation.
5. Inability to Detect Differential Pressure Sticking
Problem:
A reliable load cell helps detect differential pressure sticking, which can be hard to manage without accurate load readings.
Consequences:
Undetected differential sticking can block the wellbore and lead to lost production time.
Solution:
Adjust fluid properties to prevent sticking and closely monitor pump pressure and torque for indicators of sticking.
Load cell failures in coiled tubing milling can disrupt WOB control and increase risks of tubing fatigue and blockage. Operators should rely on secondary indicators like pump pressure, torque, and tool wear observations to make adjustments. Proactive monitoring and conservative approaches help mitigate load cell issues, ensuring safer and more efficient operations even without real-time load data.