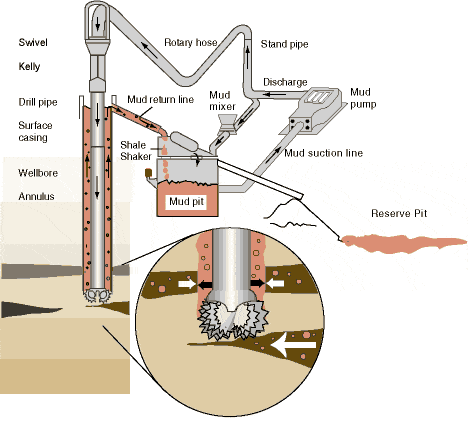
How Rotary Drilling Works
Rotary drilling operates by continuously rotating a drill bit attached to a drill string, which penetrates the subsurface formations. A drilling rig provides the necessary power to rotate the bit, apply weight, and circulate drilling fluid. The drilling fluid, or mud, is pumped down the drill string to cool the bit, carry cuttings to the surface, and maintain well pressure.
Key Components of Rotary Drilling
1. Rotary System
Converts power into rotational motion to turn the drill bit.
Includes components like the rotary table (or top drive), kelly, and drill pipe.
2. Hoisting System
Supports and controls the drill string’s movement in and out of the well.
Composed of the derrick, draw works, and traveling block.
3. Circulatory System
Pumps drilling fluid to lubricate the bit and remove cuttings.
Includes mud pumps, drill pipes, and mud tanks.
4. Bit and Drill String
The drill bit cuts through rock, while the drill string transfers power and weight.
Various bit types (e.g., roller cone, PDC) are used depending on formation hardness.
5. Blowout Prevention System
Ensures well control by preventing uncontrolled fluid flow (blowouts).
Consists of blowout preventers (BOPs) and other safety equipment.
Types of Rotary Drilling
1. Conventional Rotary Drilling – Uses a rotary table to turn the drill string.
2. Top Drive Drilling – Utilizes a motorized top drive system for more efficient rotation.
3. Directional Drilling – Allows controlled deviation of the well path to reach specific targets.
4. Extended Reach Drilling (ERD) – Enables drilling long horizontal sections to access remote reservoirs.
Advantages of Rotary Drilling
High efficiency – Enables faster penetration of formations.
Versatility – Can be used for vertical, directional, and horizontal wells.
Improved well control – Drilling mud maintains pressure and stability.
Deeper well access – Allows drilling to depths exceeding several thousand meters.