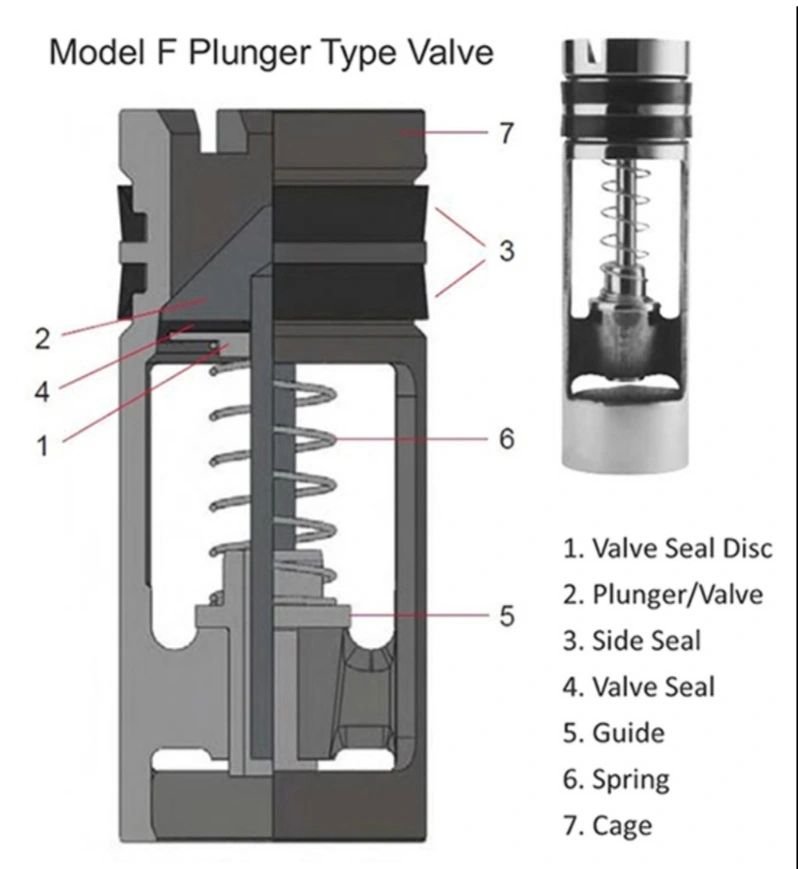
The float valve (check valve or float valve) is a critical component in a downhole motor used in directional drilling. Its main function is to prevent the backflow of drilling mud when circulation is stopped, protecting both the motor and the formation:
Reasons for its importance:
*1. Reverse flow prevention:
Prevents mud from flowing back from the well into the motor, which can cause damage to internal components or contamination of the drilling fluid.
*2. Downhole motor protection:
By preventing cuttings-laden mud from entering the motor when there is no circulation, premature wear of internal components such as bearings and power section is reduced.
*3. Improved drilling efficiency:
Maintains pressure within the system, which helps prevent problems such as string collapse or cuttings buildup on the bit.
*4. Reducing the risk of kick:
In wells with high pressure zones, the float valve helps control the flow of formation fluids towards the drill string, reducing the risk of a fluid well or a blowout.
*5. Ease of changing tools:
Allows tools to be disconnected and connected without mud spilling into the drilling string, facilitating maintenance operations or component changes.
There are different types of float valves, such as the plunger type and the flapper type, each with advantages depending on the type of operation and well conditions.
– Plunger Type:
*Design: Uses a spring-loaded plunger that moves up and down within a cylinder.
*Operation:
It opens when mud flows down through the drill string.
It closes automatically when circulation stops, thanks to spring pressure or gravity.
*Advantages:
Tighter sealing, providing better control of reverse flow.
More resistant to high pressures and harsh environments.
*Disadvantages:
It can cause greater flow restriction when open.
More prone to blockages due to mud particles or solids in the fluid.
– Flapper Type:
*Design: It has a hinged flapper that opens and closes according to the flow of the mud.
*Operation:
It opens when the fluid flows downwards.
Automatically closes by gravity when circulation stops.
*Advantages:
Less restriction to flow, which improves hydraulic efficiency.
Easier to clean and less prone to clogging.
*Disadvantages:
May not seal as tightly as plunger type.
Less effective in applications where immediate hermetic closure is required.
Which one to choose?
-Plunger Type: Preferred in wells with high differential pressure or where a tighter seal is needed to prevent kick.
-Flapper Type: It is ideal for operations where flow efficiency is more important and such a tight seal is not required.